Thinking Outside the (Gift) Box at Goodwill of the Heartland
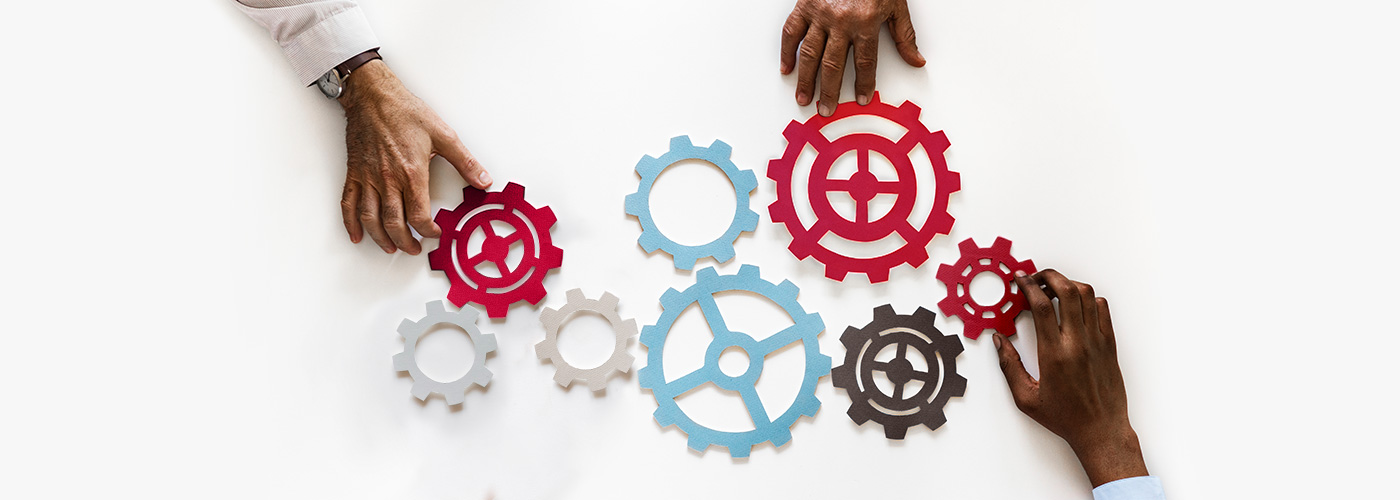
'Tis the season of giving, which also makes it the season of gift wrapping! One of the nation's most recognizable retailers gets its gift boxes from a SourceAmerica nonprofit member. Goodwill of the Heartland employs professionals with disabilities to make the Nordstrom gift boxes that will hold holiday presents across the U.S.
This year, Goodwill of the Heartland partnered with us to find ways to improve the efficiency of their manufacturing process. The results were magical!
Collaborating toward a solution
Our member agencies are dedicated to success. As Goodwill of the Heartland reflected on the 2018 holiday season, they asked one big question: How can we improve the efficiency of gift box production in 2019?
Change is often difficult. Nonprofits often have limited resources, which is a particular challenge during times of change. By joining our network, they have access to many resources and programs that can make change a little easier. The team at Goodwill of the Heartland learned about SourceAmerica's productivity engineering program and they jumped into the experience with open minds!
Our engineers made their way to Iowa for a visit. They brought with them outside perspectives and ideas to share with the Goodwill team. Together, they looked at what was working and what wasn't. Then it was time to put the work into action.
The Engineering Process
Every engineer knows the first step to any solution is identifying the challenges. Goodwill of the Heartland's program has gone through major changes and transitions, making this an important time to look at solutions to benefit their organization, employees and client.
Challenge #1:
Too many employees weren't being used to their full abilities.
Solution #1
Properly forecasting for the year ahead was key in solving the first challenge. Our engineers looked at the number of seasonal employees and the amount of gift boxes they were making. The daily quota for the facility was 500 boxes each day. That meant that only five people needed to work on any given day – a big surprise for our engineers and the Goodwill team! Until this review, between 10 and 15 employees were being assigned to do the work. That meant many of those team members weren't being used to their full abilities. Better forecasting meant that the workers who normally handle the Nordstrom contract could manage the expected volume without the help of additional seasonal team members.
Challenge #2
Each process had too many steps.
Solution #2
Part of the engineering process was looking at every step of the operation, including feedback provided by the people working on the contract. One of the Goodwill team members had an “Aha!” moment by realizing there was a “box crushing” step that was crushing productivity! Removing this step meant employees could move along the process faster and more efficiently.
Challenge #3
Too much space was dedicated to one operation.
Solution #3
With the correct number of employees and a more efficient process, our team reviewed the batching and materials. By keeping a lower volume of work-in-process on the floor, materials would be ready for shipping almost immediately. The Goodwill team working with our engineers worked with the operators to condense and streamline the entire process – a key objective in lean manufacturing. This made for happy employees!
The solution at work
The results from the collaborative review process were impressive:
- Used floorspace was reduced by 63%.
- The amount of time the material spent on the floor was reduced by 88%.
- Seasonal labor assigned to the project was reduced by 40%.
- With business demand being so high, Goodwill of the Heartland has reassigned many of the employees to other areas throughout the organization.
The power of collaboration
Goodwill of the Heartland has a few tips for other nonprofits in our network.
- Use the resources available and provided by SourceAmerica!
- Identify people in your contracts who will champion change. Suggestions can be made, but without someone anyone to implement them, it's hard to make progress.
- Engage your entire team in the process and be transparent with SourceAmerica productivity engineers.
- SourceAmerica had provided Productivity Engineering with budget to help implement the improvement.
Our entire SourceAmerica team enjoys seeing the success Goodwill at the Heartland is having, and we can't wait to hear about their results for this holiday season!
To learn more about our productivity engineers contact productivityengineering@sourceamerica.org.